Supporting Our Customers Is A Key Priority.
The largest advance was 4 years ago when we eliminated the hydraulic system on the machine that provided the cross travel motion. We have replaced it with a stepping motor and ball screw system, and a color touch screen. In addition to the lower maintenance costs with the hydraulic cylinder elimination, the stepping motor traverse allows for programmable cross travel rates and multiple rates of cross travel.


For templates with deeper forms or for customers running autoloading systems, we offer an auto dressing system that is low cost and provides automatic compensations on a servo cycle machine and Hi-Accuracy systems. This system frees up a technician or operator when re-dressing deep forms into the wheel. Program the number of passes and walk away to do other tasks.


We also offer two different types of CNC Dressers, over the wheel which solely uses single point diamond technology or Horizontal which uses both single point diamonds or rotary diamond disks to dress conventional abrasive or super abrasive wheels. The over the wheel two axis system is a robust system that has .1 micron encoders for both axis and is programmed by Microsoft excel wizards. The Schneeberger rails and linear motor technology makes for smooth, accurate and ridged dressing. This is also an ideal fit for dress-able super abrasive technology, automatic dressing and compensations.


The horizontal CNC is a very popular option for our machines. It allows for rotary diamond disk dressing with a 6” diameter disk. The .1 micron Heidenhein absolute encoders on both axis makes dressing as close to perfection as possible. Using Schneeberger bearing rails and linear motor technology it is again a smooth and robust system. The rotary diamond disk is powered by a parker servo motor giving infinite variables for dressing speeds and direction. Programmed by Microsoft Excel wizards, programming is simple and seamless—attach the dress program to your grind profile program. We have also partnered with Schmitt Industries in providing an SBS Dynamic Wheel Balancer with Acoustic Emission Gap Elimination and Analysis Tool. This equipment can be installed to provide the best vibration analysis and control of the grinding wheel balance and eliminating non contact dressing passes of the CNC Wheel Dressers. Royal Master has also developed a machine specifically for the offline dressing of grinding wheels.




Pressurized wheel washer is a wheel maintenance option that is particularly helpful when grinding plastics and the grinding wheel loads up with material. Instead of dressing the wheel and having to perform maintenance tasks such as sanding, the wheel cleaner removes the free abrasives from the wheel matrix and cleans the material embedded in the wheel. Available on new machines or retrofits, it is a feature that helps in keeping the machine productive in this type of application.



Automatic Grinding Wheel Balancing and Acoustic Emissions

Dressing Option Videos
Want More ?
Other Wire Grinding Solutions

TG-12×4 and TG-12×8 Servo Cycle Grinding Systems
The most versatile machine for up to 5 taper wire grinding
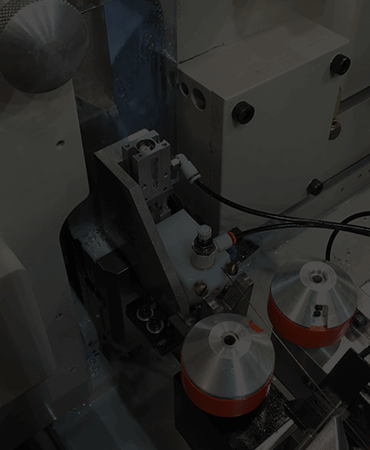
Automation of Guidewire Grinding
Operator Assist Devices to Fully Robotic Multitasking Solutions
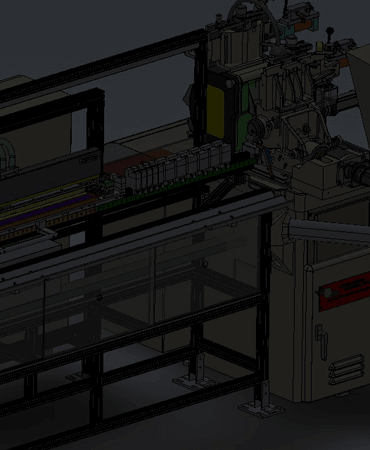
Generation 5.8 Production Guidewire Grinding System
The machine that revolutionized the wire grinding industry is still producing millions of wires per year worldwide
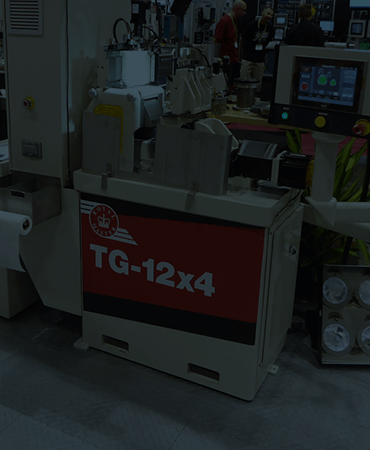