Supporting Our Customers Is A Key Priority.
Over 10 years ago a prominent Dental company approached us to grind a unique fiber glass product called a fiber post. These parts were discussed and it quickly became apparent that they had simple geometries as well as complicated ones. The more simple ones were a no question fit for a TG-12x4 with a bowl feeder. The more complicated ones were a god fit for our GX machine. Using plated diamond wheels, these more complicated geometries were ground quickly with a superb surface finish. During the installation of the first machine the question quickly became “can this machine run all night without an operator?” On the first night we tried it, the answer was yes in the morning when we came in. With over 25 machines sold around the world making these products we have become the company that is the go-to for fiber post grinding.
The grinding of Fiber posts is a simple process. There are two basic approaches as mentioned above. The one process uses cut to length parts, and the second uses long rods, usually 1-2 m long.
The TG-12x4 Fiber Post System
The TG-12x4 machine Fiber posts are normally started with extruded and ground poles, between 1-2 m long, and cut to their final length. These pieces are then placed in a vibratory bowl feeder, and fed into a feeder that will inject them one at a time into the centerless grinder. Part to part cycle time is about 8 seconds.
The shape of the post is transferred into the part by way of the grinding wheel. The grinding and regulating wheel use templates that are located over the wheels. These templates have the shape of the form to be dressed into the wheels. Using a diamond and a stepping motor for cross travel the shape that is in the template is transferred into the wheel.
This method grinding is efficient and operator free. It also has the ability to run overnight unattended.
The Generation X Fiber Post System
The Generation X System is a completely different approach, it requires less up front material preparation for the grinding operation. Rather than having to cut the material to the final part length the rods of 1-2 meters are introduced to the machine, and during the grinding process, they are ground to their final shape and then cut. When the rod is exhausted with pieces, the is a 4” piece of scrap left for recycling. The great part of the GX set-up is multiple part configurations can be easily ground by recalling the recipes from the machine control. Changeover from part to part can be as quick as 5 minutes.
For longer run simple profiles, super abrasive wheels are used with the shape already preformed into the wheel. These plated diamond wheels can be made in any shape provide for easy changeovers when a wheel change is needed
When using the GX machine, a magazine type feeder is used that can hold approximately 75 1-2m long rods. This is plenty for an overnight unattended run.
More exotic profiles can be ground on the GX due to its three axis capability. In addition to conventional cylindrical shapes, cam shapes can also be made.
THE GENERATION X
OTHER DENTAL SOLUTIONS
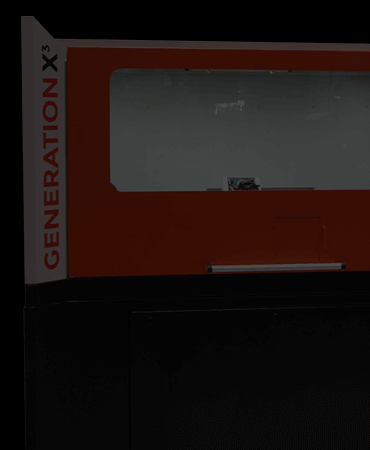