Supporting Our Customers Is A Key Priority.
Royal Master redefines the manufacturing of Endodontic Files with our GX3 machine. Grinding from raw material to fully finished file with MM markers and palletizing in less than 60 seconds part to part is a huge leap for an industry looking for higher productivity at a more competitive price point then current options available worldwide.
With a highly successful GX machine, a customer approached us to discuss a new opportunity. The grinding of endodontic files. At first, we discussed the preprocesses before they would twist the files. Two options were to blank out the files or grind the flats on them prior to twisting. It wasn’t very long before we figured out how to add three more axis to the system to achieve the grinding of the flutes into the files. After some initial samples, the launch customer ordered a package of three machines, and the rest was history.
In September of 2018 we will be introducing the second generation of the system at IMTS. This second generation was sparked by the initial launch customer’s feedback in looking for a more ergonomic design that took up less floor space. With this in mind, and feedback from other GX 3 customers worldwide, we embarked on the design of the second-generation system.
This machine differentiates itself from other world wide options by:
- Grinding a complete NiTi File ( Blade) with all features including millimeter markers from a spool of raw material in less then 55 seconds
- No Requirement for a pre-grind
- Low consumable cost per blade depending on profile
Axis Definitions
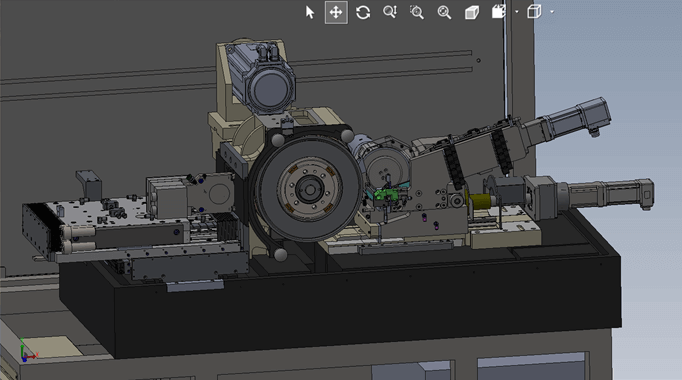
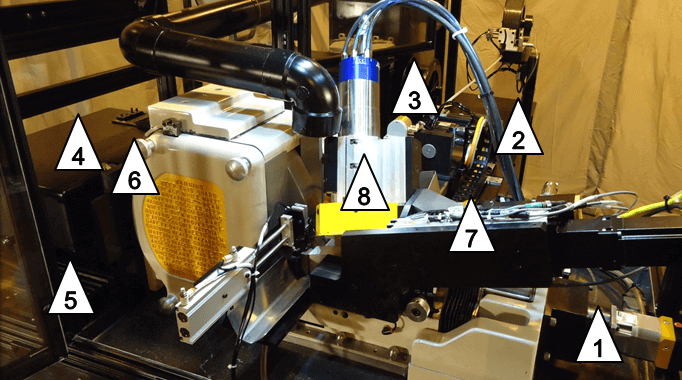
8 AXIS OF COORDINATED MOTION AND THEIR DEFINITIONS
Specifications | |
---|---|
Axis 1 | Diameter Axis for Taper Grinding .1 Micron Resolution |
Axis 2 | Material Feeding / Length Dimensions .1 Micron Resolution |
Axis 3 | Collet Rotation (Servo Driven) |
Axis 4 | CNC Dresser X axis (When Equipped with a CNC Dresser. When using Plated Wheels it is not necessary) |
Axis 5 | CNC Dresser Z axis (When Equipped with a CNC Dresser. When using Plated Wheels it is not necessary) |
Axis 6 | CNC Dresser Rotary Diamond Disk Axis (When Equipped with a CNC Dresser. When using Plated Wheels it is not necessary) |
Axis 8 | Fluting Axis rotation -5 to 90 Degrees |
How The GX3 Works
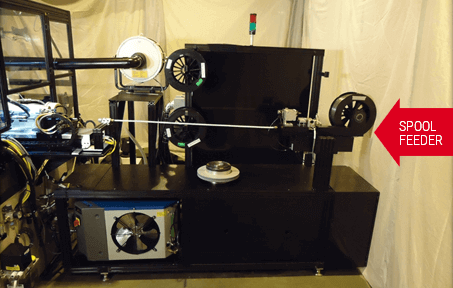
First Step
- Raw material is delivered to the machine from a spool mounted inside of the machine. The material is un-spooled to a predetermined length, and cut. This can be up to 5m long.
- There is a 5” (127mm) piece of scrap for every bar cut.
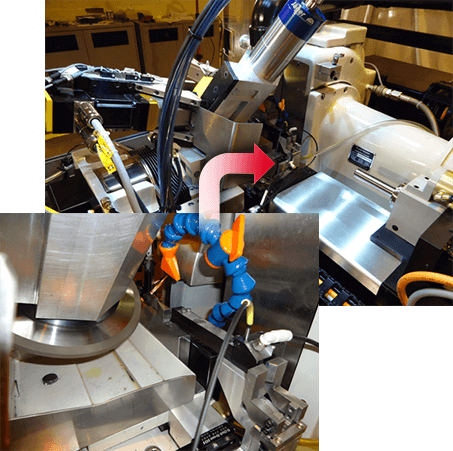
Next Step
After the material is cut, the machine references the tip of the cut material by a photo eye. This will determine the datum of the material.
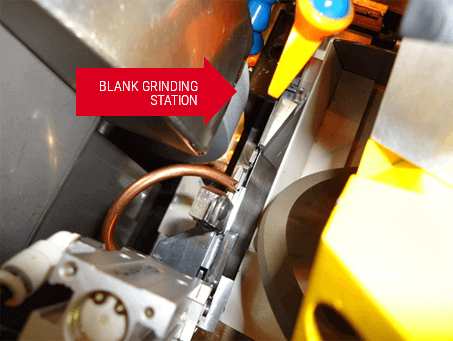
Grinding the Blank
After the material is cut, the machine references the tip of the cut material by a photo eye. This will determine the datum of the material.
- The part fed into the tapered part of the wheels slowly to evenly take the stock removal off the part, then finish ground on the taper
- The part is indexed to the MM marker portion of the wheel and they are plunge ground
- Oil is used as a coolant to keep the part cool and the material from loading into the grinding wheel
- Whatever Shape is in the wheel is ground into the part
- The part that was just taper ground that is still attached to the entire rod is indexed by way of the .1 micron linear motor to the helical station just before the tip of the Endofile
- Axis 8 will set the angle from -5 to 90 degrees, and the Axis 7 will move forward.
- The wheel, 6” in diameter, diamond in composition will engage with the part at 3500 – 10,000 rpm RPM.
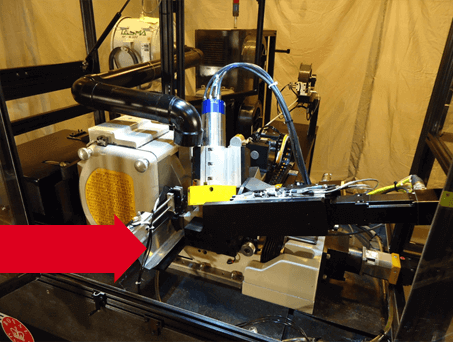
They come out of here…
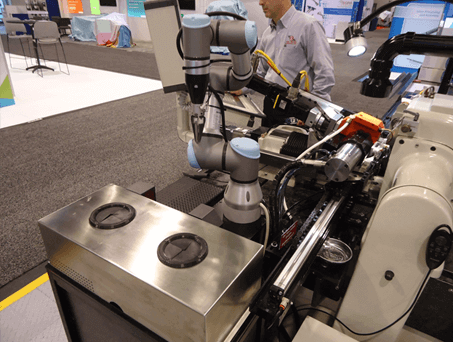
With The Un-loader and a Collaborative Robot we can Palletize the Parts for easier Handling
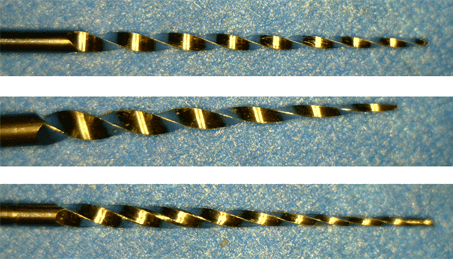
One – Four Start Helix
If your Grinding a File with a three or four start Helix, the one helix will grind, the linear motor will retract the part, and the collet head will index. The part will begin grinding again.
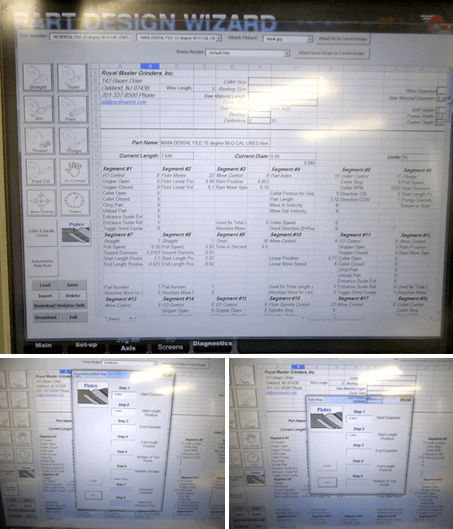
Programming is Done by
MS Excel
The GX3 in action
Other Dental Solutions
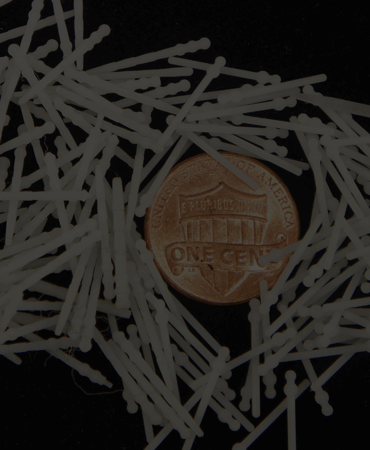